数控钻孔编程步骤,听起来可能有些专业,但实际上,只要你跟着步骤一步步来,你会发现这其实并不复杂。想象你正站在数控机床前,准备为一块钢板钻孔。你知道该怎么做吗?别急,这就为你详细讲解数控钻孔编程的每一个步骤。
一、准备工作:选择合适的工具和参数
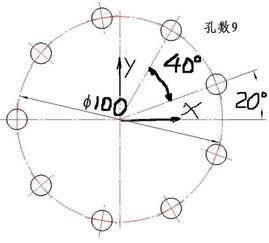
在开始编程之前,你需要选择合适的钻头和夹具。不同的材料需要不同的钻头,比如钢、铝或是硬质合金。选对了钻头,才能保证加工过程的顺利进行。接下来,确定合适的切削速度和进给速率,这对防止工具过早磨损和保证加工质量至关重要。润滑和冷却也是不能忽视的环节,适当的润滑可以减少摩擦,提高切削性能。
二、定义工件零点
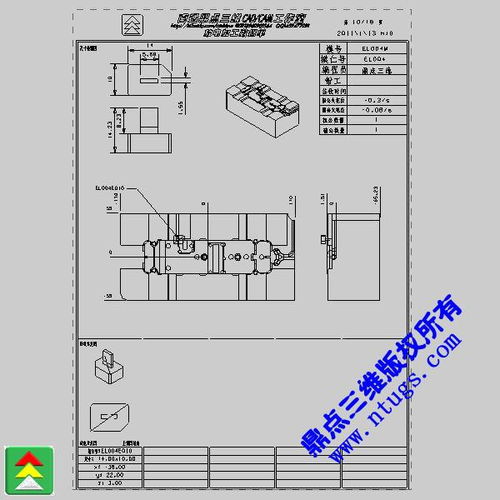
工件零点的设定直接关系到钻孔加工的准确性。在数控钻孔编程中,你需要明确工件的参考点,即程序的起点。一般来说,工件零点的选择依据工件的具体尺寸和加工要求来确定,常见的有工件的中心点、一角或是特定平面。准确设定零点,是精确加工的基础。
三、设定钻孔路径
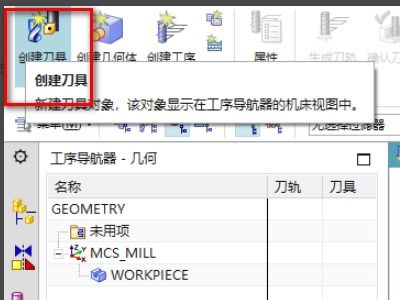
在编程过程中,钻孔路径的设置是影响加工效率和质量的重要环节。有效的路径规划可以最大限度地减少走空行程,提高加工效率。更重要的是,合理的路径设定可以避免工具过度磨损和损坏,延长工具寿命。钻孔路径不仅包括钻孔的顺序,还包括钻入和撤出的方式,不同材料和孔深会有不同的策略。
四、编写相应的数控代码
根据以上准备和设定,最后一步是编写数控程序代码。这个步骤需要遵循特定的G代码或M代码规约,反映出之前各个步骤的设定,包括工具号、刀具参数、钻孔位置和深度等。编写代码时,要确保每一个指令都准确无误,因为一个小小的错误都可能导致加工失败。
五、导入加工程序和设置工件
将编写好的加工程序导入数控机床的控制系统中。可以通过USB接口、以太网等方式将程序传输到数控机床。导入成功后,将工件安装在数控加工中心的工作台上,并根据设定的程序,对工件进行合理的夹持和定位。然后设置坐标系,确定加工的起始点和坐标原点。
六、调试程序和进行自动加工
在运行加工程序前,进行一次手动操作的试切,确保加工路径的正确。通过手动模式,逐步验证加工路径的正确性和机床的可运行性。确认程序和机床运行正常后,可以切换到自动加工模式,开始进行钻孔加工。数控机床根据预设的程序和参数,自动进行钻孔操作。
七、检验加工结果
在加工完成后,检查钻孔的尺寸和质量是否符合要求。使用测量工具(如卡尺、测微计等),检测钻孔的直径、深度和位置精度。如果发现任何问题,及时调整程序或操作,避免类似问题再次发生。
八、保存加工参数和结果
将加工参数和结果记录下来,作为以后的参考使用。可以将加工参数和程序保存在计算机中,以备下次使用。这些步骤是编程钻孔的基本流程,具体操作还需要根据具体的加工设备和软件来进行调整。在进行加工操作时,一定要注意安全,遵循相关操作规程。
通过以上步骤,你就可以顺利完成数控钻孔编程。虽然这个过程看起来有些繁琐,但只要多练习几次,你就能熟练掌握。数控钻孔编程不仅能够提高加工效率,还能保证加工质量,是现代制造业中不可或缺的一项技术。所以,不妨从现在开始,一步步学习,掌握这项技能吧!